Grain Handling
Skyway Grain Systems Inc. knows that every farm facility is different in many ways, and it takes a complete line of quality vendors to meet those needs. Our years of experience and knowledge can offer a professional service to small farm operations with a 2-3 bin operation, all the way to the large farm operations with commercial size bins and high-capacity throughput. No matter the size of your operation our dedicated team can make your farm site a first-class operation.
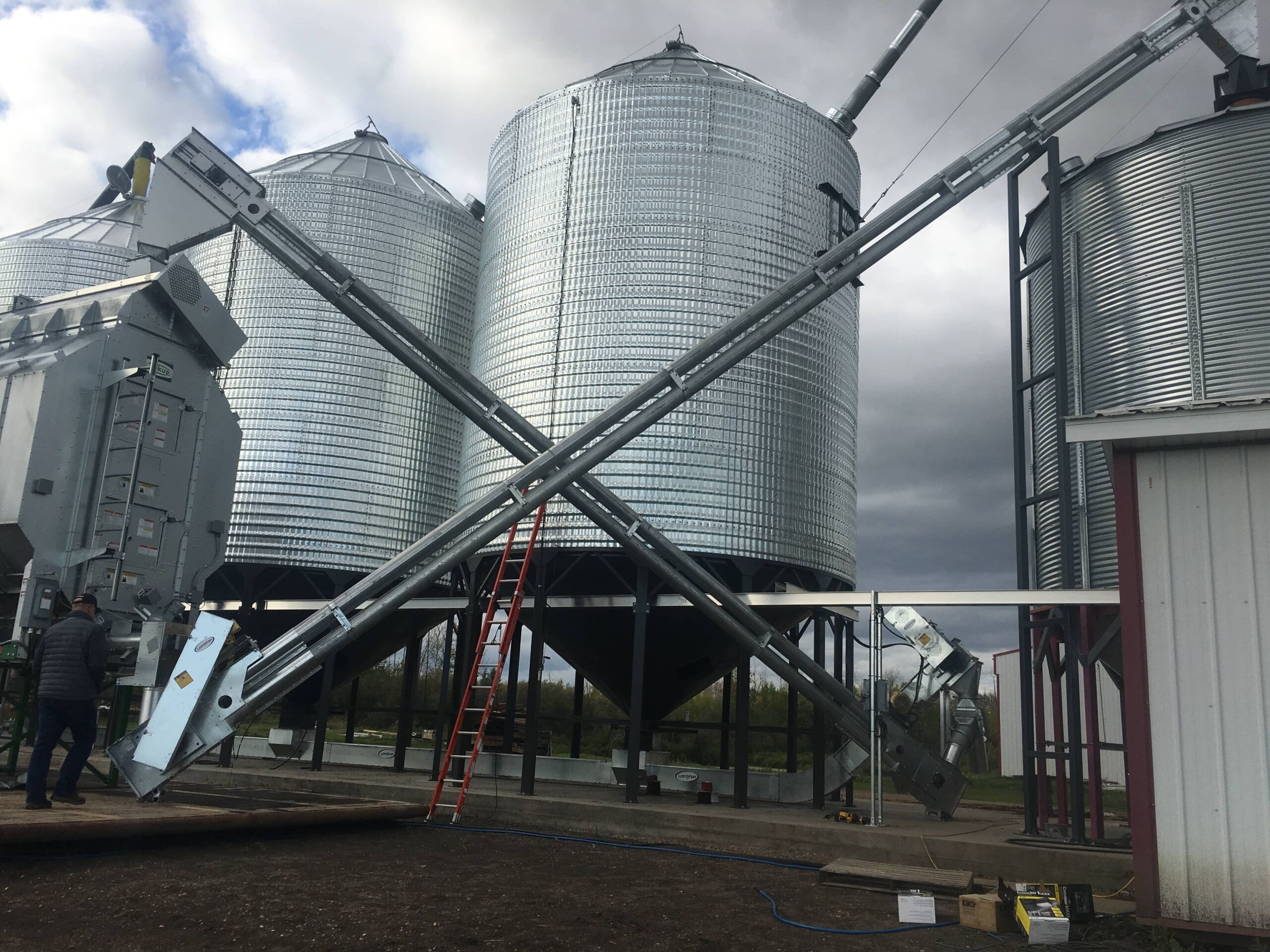